
Solution for Manufacturing Industry
Calibration, an often overlooked yet indispensable facet of the manufacturing and process industry, serves as the bedrock for precision, reliability, and operational excellence.
Why Calibration is Essential for the Manufacturing and Process Industry?
In this fast-paced and highly competitive sector, where even the slightest deviation can have profound consequences, calibration emerges as the linchpin ensuring the accuracy of measurement instruments and equipment. Whether it’s temperature, pressure, or dimensional measurements, calibrated instruments form the backbone of quality control and regulatory compliance, influencing every aspect of the intricate web of manufacturing processes.
Manufacturing and process industries operate within stringent parameters, demanding a level of precision that leaves no room for error. In this context, calibration becomes essential, acting as a proactive measure to maintain the accuracy of measurement instruments. From ensuring the proper functioning of machinery to guaranteeing the consistency of product dimensions, calibration lays the foundation for optimal performance and quality assurance.
Challenges faced without proper calibration in the manufacturing and process industry
The manufacturing and process industry faces a myriad of challenges when calibration is neglected, each with the potential to disrupt the entire production ecosystem.
1. Inaccurate measurements:
One of the primary challenges lies in inaccurate measurements, which can lead to faulty production processes and the creation of defective products. In a sector where product quality is synonymous with brand reputation, the consequences of subpar calibration can reverberate far beyond the manufacturing floor, affecting customer satisfaction and loyalty.
2. Non-compliance with standards:
Moreover, the absence of proper calibration poses a substantial risk of non-compliance with industry standards and regulations. Regulatory bodies, recognizing the critical role of calibration in ensuring safety and quality, mandate adherence to specified measurement standards. Failure to comply not only jeopardizes the standing of a company within the industry but can also result in legal repercussions, adding a layer of complexity to an already intricate operational landscape.
3. Increased waste and compromised safety standards:
In an industry that relies heavily on precision and efficiency, the impact of these challenges extends to increased waste, higher production costs, and compromised safety standards. Downtimes become more frequent, and the overall reliability of the manufacturing process comes into question. These challenges highlight the interconnectedness of calibration with the seamless functioning of the manufacturing and process industry.
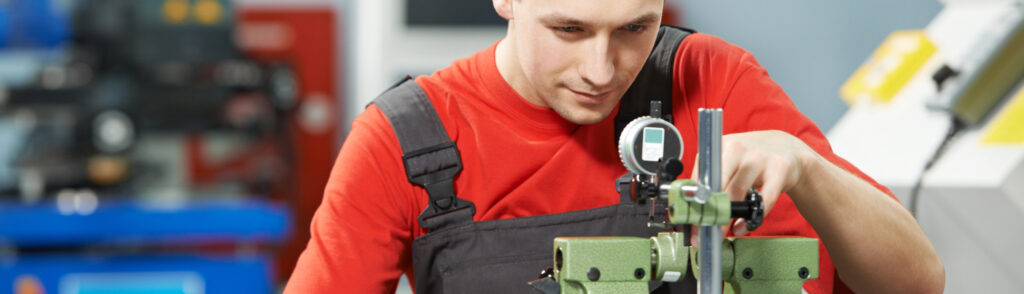
BENEFITS OF CALIBRATION
Addressing the challenges posed by the lack of proper calibration requires the implementation of robust calibration solutions tailored to the specific needs of the manufacturing and process industry. The journey towards precision begins with a comprehensive understanding of the various types of measurement instruments used in the industry, ranging from thermocouples and pressure gauges to sophisticated dimensional measurement tools.
Regular calibration of these instruments ensures that they consistently provide accurate and reliable readings, forming the basis for informed decision-making throughout the production cycle. By incorporating advanced calibration technologies and methodologies, manufacturers can not only meet but exceed industry standards, positioning themselves as leaders in quality and compliance.
Benefits 1 – Assurance of product conformity
The benefits of calibration in the manufacturing and process industry are multifaceted and extend beyond the realm of simple accuracy. One of the primary advantages lies in the assurance of product conformity to established standards. This not only meets customer expectations but also cultivates a sense of trust and loyalty, essential for sustained success in a competitive market.
Benefits 2 – Reduction of production errors
Additionally, calibrated instruments contribute significantly to the reduction of production errors, minimizing waste and maximizing resource utilization. The economic implications of improved accuracy are substantial, with operational costs decreasing as a result of optimized production processes. This, in turn, enhances the overall efficiency and profitability of manufacturing operations.
Benefits 3 – Improved product performance and reliability
Moreover, the emphasis on accuracy in measurements translates directly to improved product performance, durability, and reliability. In industries where the integrity of products is paramount, calibration emerges as a strategic investment in long-term success. Products that consistently meet or exceed quality standards become a hallmark of the company’s commitment to excellence, fostering a positive brand image in the market.
Benefits 4 – Compliance and documentation
Furthermore, compliance with industry regulations is a critical aspect of the manufacturing and process industry. Calibration ensures that all measurements align with established standards, safeguarding the company against legal repercussions and reinforcing its commitment to quality and safety. The documentation and traceability aspects of calibration further facilitate the audit process, easing the burden of regulatory compliance for manufacturers.
In conclusion, calibration stands as a cornerstone in the manufacturing and process industry, playing a pivotal role in maintaining precision, quality, and compliance. The consequences of neglecting calibration can be detrimental, leading to suboptimal production processes, defective products, and potential legal ramifications. Embracing calibration solutions not only addresses these challenges but also unlocks a host of benefits, including enhanced product quality, increased efficiency, and adherence to industry standards.
In an industry where accuracy is synonymous with success, calibration emerges as an indispensable practice for ensuring the seamless functioning and sustained excellence of manufacturing and process operations. As manufacturers navigate an increasingly complex landscape, the strategic integration of calibration into their processes becomes a competitive advantage, setting the stage for innovation, growth, and enduring success.
Calibration, often viewed as a routine task, reveals itself as a dynamic force shaping the future of the manufacturing and process industry, where precision is not just a goal but a non-negotiable requirement for those striving for excellence.