
Solutions for Food Industry
Calibration is indispensable in the food and beverage industry because it underpins product quality, safety, regulatory compliance, cost-efficiency, and sustainability.
Why calibration is essential for the food and beverage industry?
In the fast-paced and demanding world of the food and beverage industry, where quality, safety, and precision are paramount, calibration plays a pivotal role in ensuring the accuracy of measurement instruments and production processes. From temperature control in cooking to the formulation of recipes in food processing, calibration is the linchpin that underpins product consistency, compliance with regulatory standards, and overall efficiency in the food and beverage manufacturing. In an industry where consumer trust is closely tied to the reliability of products, calibrated instruments are fundamental for producing food and beverages with precision, safety, and adherence to quality standards.
Food and beverage production involves a myriad of processes and measurements, and precision in these aspects is crucial to delivering products that meet quality and safety requirements. Calibration ensures that instruments used in manufacturing, quality control, and food safety consistently provide accurate data, contributing to the integrity of food and beverage products.
Challenges faced without proper calibration in the food and beverage industry
The food and beverage industry encounters distinctive challenges when calibration is overlooked, impacting product consistency, regulatory compliance, and consumer safety.
1. Inconsistent product quality:
One of the primary challenges lies in inconsistent product quality. Without proper calibration, production equipment may provide imprecise measurements, leading to variations in taste, texture, and overall quality of food and beverage products.
2. Compliance with food safety standards:
Calibration is crucial for compliance with food safety standards. Inaccuracies in measurement instruments can result in products that fail to meet regulatory requirements, posing risks to consumer health and potentially leading to legal consequences for food and beverage manufacturers.
3. Quality control reliability:
In the realm of food and beverage quality control, reliability is paramount. Calibrated instruments, such as pH meters and viscosity testers, are necessary for ensuring that products meet defined specifications. Without accurate calibration, compromises in quality control may occur, impacting product consistency and safety.
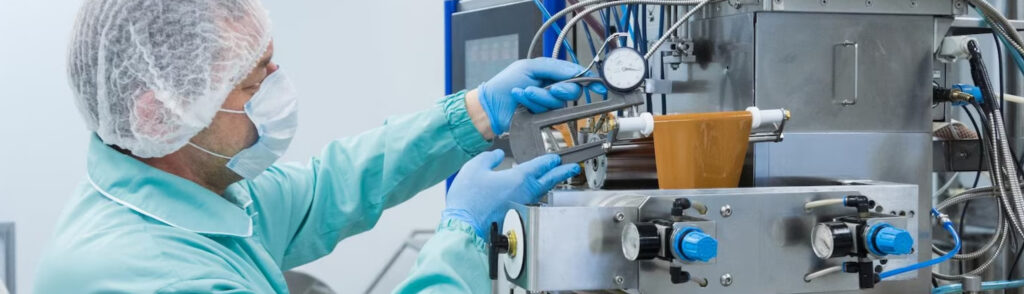
BENEFITS OF CALIBRATION
Addressing these challenges necessitates the implementation of robust calibration solutions tailored to the specific needs of the food and beverage industry.
Benefits 1 – Consistent product quality
Calibrating production equipment ensures consistent and accurate measurements, contributing to uniform product quality. This enhances consumer satisfaction, brand reputation, and overall market competitiveness.
Benefits 2 – Food safety compliance
Calibration is fundamental for meeting food safety standards. Accurate calibration of instruments ensures that food and beverage products comply with stringent regulations, safeguarding consumer health and maintaining the trust of both regulators and consumers.
Benefits 3 – Reliable quality control
Calibrated instruments in quality control processes are indispensable for maintaining high standards of product quality. Accurate measurements from calibrated devices, such as pH meters and viscosity testers, contribute to consistent product performance and safety.
Benefits 4 – Cost-efficiency and consumer trust
Calibration contributes to cost-efficiency and consumer trust. Accurate measurements facilitated by calibrated instruments reduce the likelihood of batch failures, minimizing production costs and building trust among consumers who expect reliable and consistent food and beverage products.
In conclusion, calibration stands as a cornerstone in the food and beverage industry, playing a pivotal role in ensuring precision, safety, and quality in food and beverage manufacturing. The challenges posed by inaccurate measurements have profound implications for product consistency, food safety, and consumer trust. Embracing robust calibration solutions tailored to the unique requirements of the food and beverage industry not only addresses these challenges but also unlocks a spectrum of benefits.
From consistent product quality to food safety compliance and enhanced reliability in quality control, calibration is the key to unlocking the full potential of the food and beverage industry. As the industry continues to evolve to meet changing consumer demands, calibration becomes a strategic investment for food and beverage manufacturers striving to achieve optimal product quality, regulatory adherence, and consumer satisfaction. Calibration, often working behind the scenes, emerges as a dynamic force shaping the future of the food and beverage industry, where precision is not just a standard but an essential element in delivering safe, consistent, and high-quality products to consumers around the world.